Un centru de prelucrare orizontal care oferă o capacitate de productivitate remarcabilă, de la o capacitate de prelucrare copleșitoare și o fiabilitate incredibilă
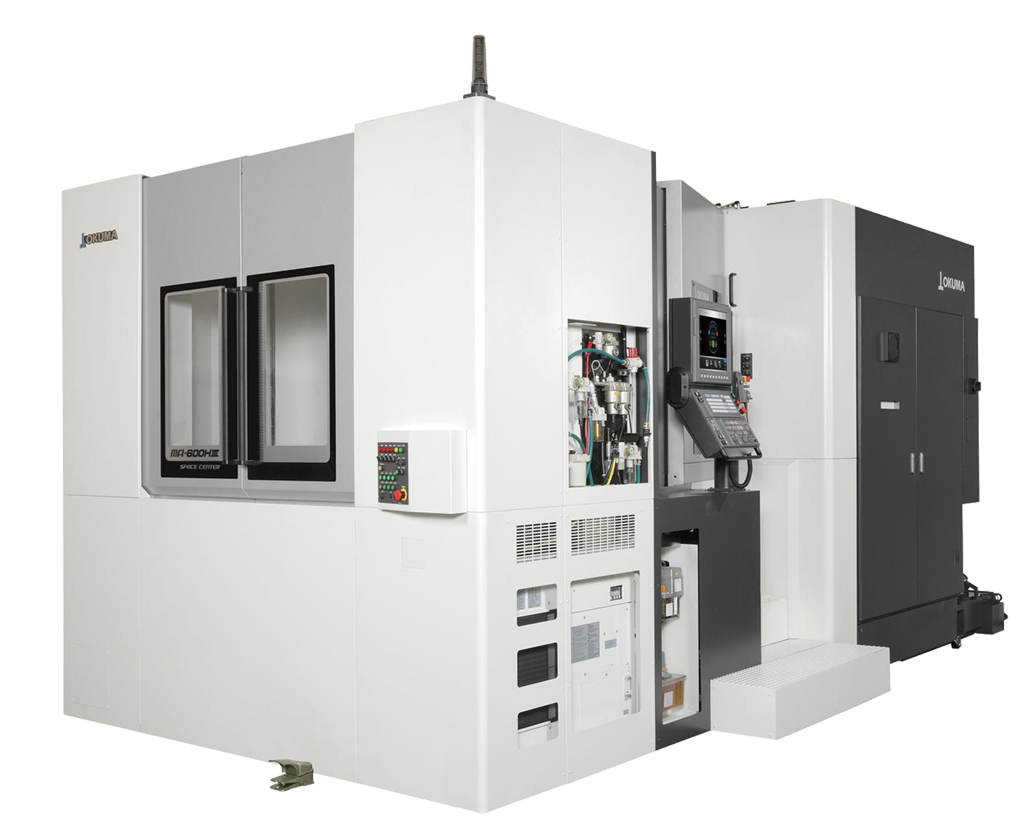
Noul centru de prelucrare de ultimă generație care se alăture gamei de centre de prelucrare orizontale OKUMA. Acest centru orizontal de prelucrare OKUMA MA-600HIII – oferă capacități de prelucrare la un alt nivel oferind câteva funcții noi.
Caracteristici de bază ale centru orizontal de prelucrare MA-600HIII:
- Creștere suplimentară a capacității de prelucrare cu un nou arbore principaș puternic: 10.000 min-1 (opțional)
- Productivitate mai mare cu un spațiu de lucru mai mare într-o amprentă la sol compactă
- Stabilitate dimensională remarcabilă chiar și în prelucrarea grea a pieselor mari
- Productivitate îmbunătățită prin scurtarea timpilor de non-așchiere
- Evacuare de șpan imbunătățită care crește timpul de funcționare
- „Rezervor fără depunere” îmbunătățește prelucrările stabile (opțiune recomandată)
- Sisteme de automatizare pentru a îmbunătăți productivitatea
Creștere suplimentară a capacității de prelucrare cu un nou arbore puternic de 10.000 rot/min
Manipularea unei game largi de aplicații, de la prelucrare grea până la prelucrare cu avans mare
Structura axului proiectată pentru prelucrare puternică.
Rulmenții cu role pentru față fac arborele extrem de rigid. Acest lucru permite aplicații de scule cu potențial maxim și suport solid pentru tăiere puternică.
Arbori principali disponibili:
● Noul Arbore Puternic: 10,000 min-1
● Arbore Standard: 6,000 min-1
● Arbore cu cuplu ridicat: 6,000 min-1
Durată lungă de viață oferită de toate arborele echipate cu sisteme de lubrifiere ulei-aer.
Sprijină o gamă mai largă de aplicații cu o nouă gamă de axuri.
Oferă capacitate mare de prelucrare într-o gamă largă de viteze mici până la mari. Manevrează eficient o gamă largă de piese de prelucrat, de la tăierea grea a oțelului până la prelucrarea aluminiului.
Productivitate mai mare a suprafeței de pardoseală cu un spațiu de lucru mai mare
Deplasări optime pentru aplicațiile cu piese mari
Centru Orizontal prelucrare MA-600HIII are cursa axei X mai lungă, iar dimensiunea maximă încărcabilă a piesei de prelucrat a crescut, de asemenea, pentru a gestiona o gamă mai largă de aplicații.
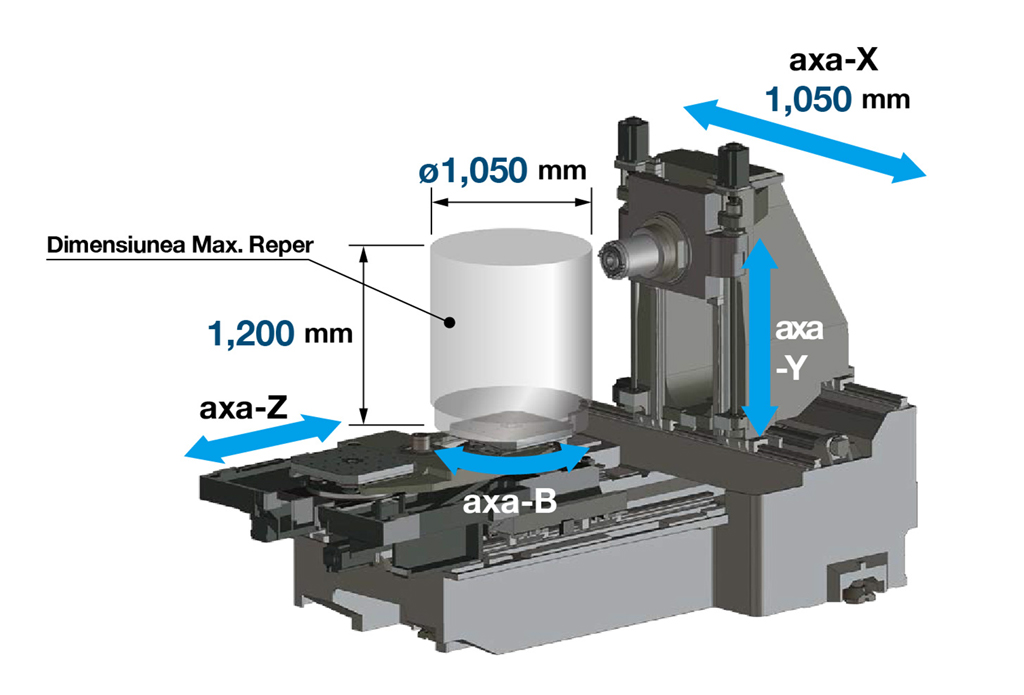
Centru Orizontal prelucrare MA-600HIII este proiectată structural pentru ușurință în utilizare
Accesibilitate bună la arbore și reperul de prelucrat
● 800 mm de la panoul de operare la arborele principal
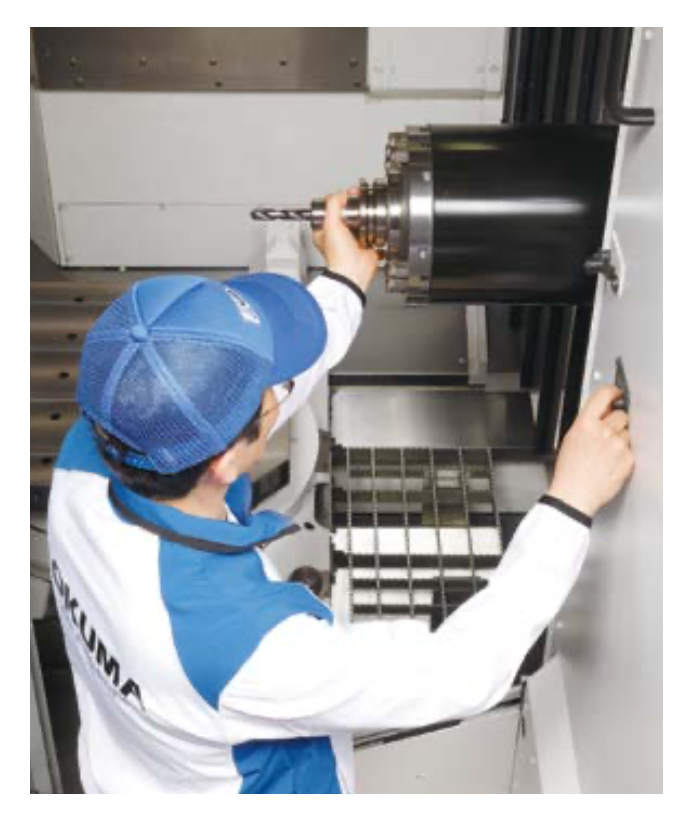
Panoul de operare montat pe stânga și mișcarea pivotantă îmbunătățește vizibilitatea și operabilitatea.
● Piesa de prelucrat și ecranul de operare cu direcțiile axelor XYZ sunt aceleași
● Operatorul poate fi aproape de ecran, pentru mai puțin efort
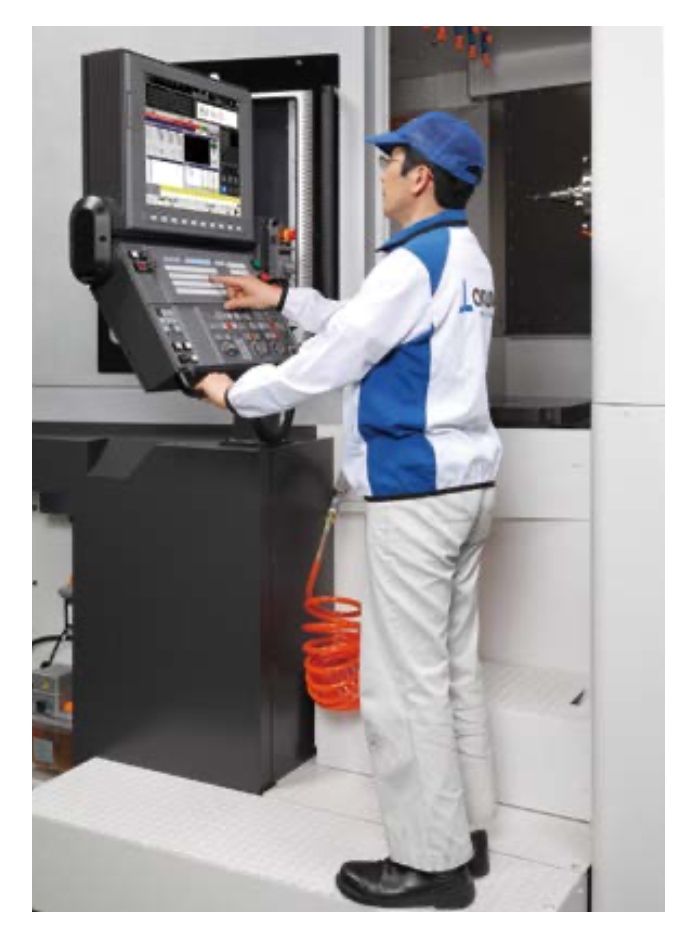
Tavan deschis pentru instalare și spațiul de lucru
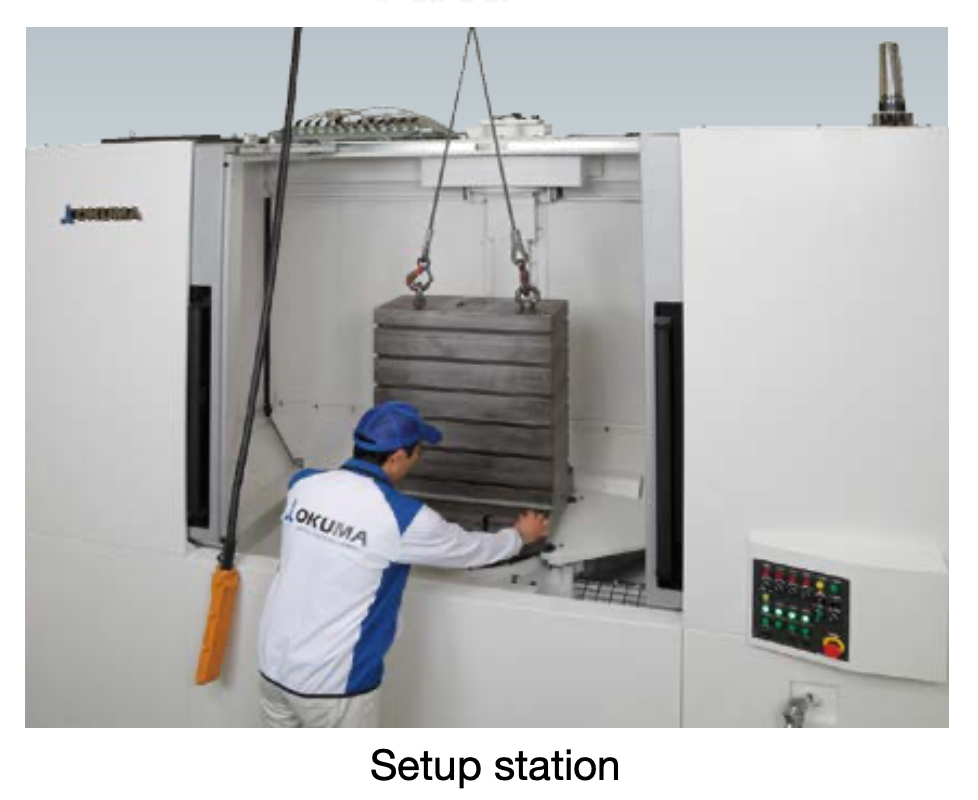
● Încărcare/descărcare parțială ușoară cu macaraua
● Iluminarea este bună, iar lichidul de răcire nu cade în zona spațiului de lucru
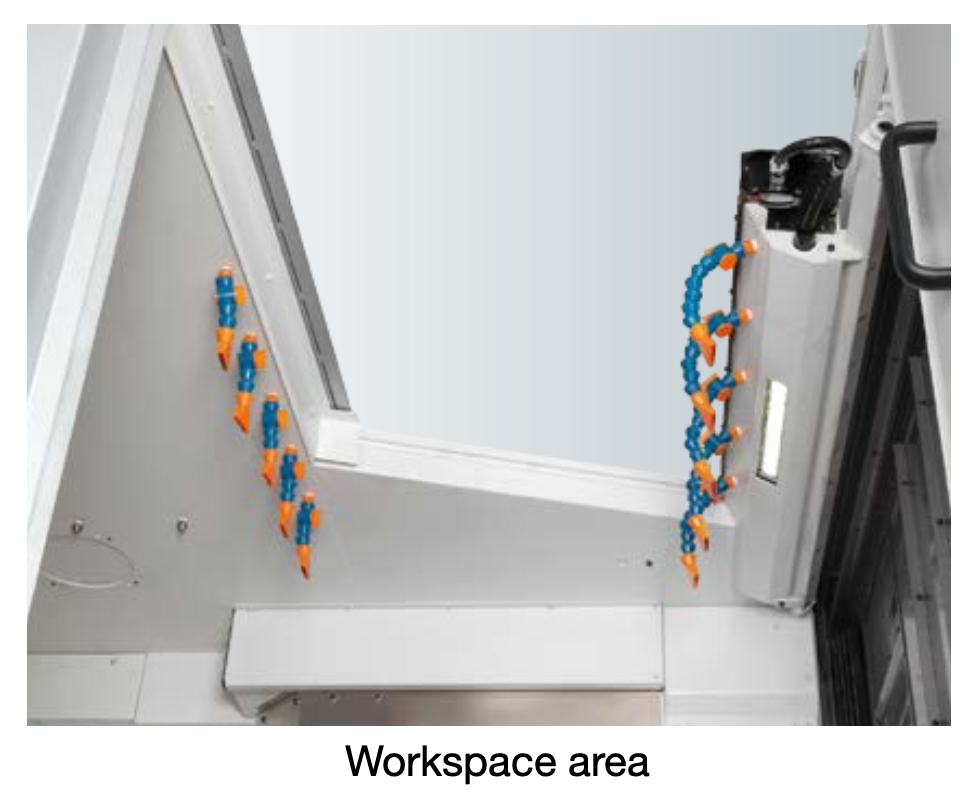
Centru Orizontal prelucrare MA-600HIII cu o precizie dimensională remarcabilă chiar și pentru prelucrarea pe termen lung a pieselor mari
Thermo-Friendly Concept
Abordarea unică de „acceptare a schimbărilor de temperatură”.
Stabilitate dimensională remarcabilă
Conceptul Thermo-Friendly de la Okuma atinge o stabilitate dimensională ridicată nu numai atunci când temperatura camerei se schimbă, ci și la pornirea mașinii sau la reluarea prelucrării. Pentru a stabiliza deformarea termică, timpul de încălzire este scurtat și sarcina corecției dimensionale în timpul repornirii prelucrării este redusă.
Mașina este proiectată structural pentru a obține o precizie remarcabilă
● Batiu susținut în 3 puncte foarte rigid
Instalare usoara datorita patului care nu se rasuceste. Sprijină o precizie stabilă și ridicată pe o perioadă lungă de timp.
● Suport șurub cu bile
Suporturile șuruburilor cu bile de la ambele capete ale axelor X-Y-Z sunt întărite și combinate pentru o conducere și o poziționare extrem de precise.
● Șurub cu bile cu răcire
Răcirea cu șurub cu bile axelor X-Y-Z și răcirea suportului motorului pe axa Y sunt standard. Asigurarea preciziei stabile în timpul ratelor ridicate de operare.
● Masă indexată și palet indexat foarte precis
• Standard: cuplare curvică (indexare de 1 grad)
• Opțional: NC (indexare 0,001 grade)
Așezarea paletului pe un con conic realizează o poziționare foarte precisă și o durabilitate excelentă.
Productivitate îmbunătățită prin scurtarea timpului non-așchiere
Sunt posibili timpi mai scurți de schimbare a sculei atunci când se utilizează lichid de răcire prin arborele principal
● Aspirarea lichidului de răcire în exces în ax Îndepărtează lichidul de răcire rezidual din sculă și ax într-o singură tragere: 0,4 secunde (datele reale de foraj). Aspirația lichidului de răcire în ax elimină necesitatea unei suflari de aer (minim 15 secunde) pentru a îndepărta lichidul de răcire rezidual, scurtând timpul de schimbare a sculei.
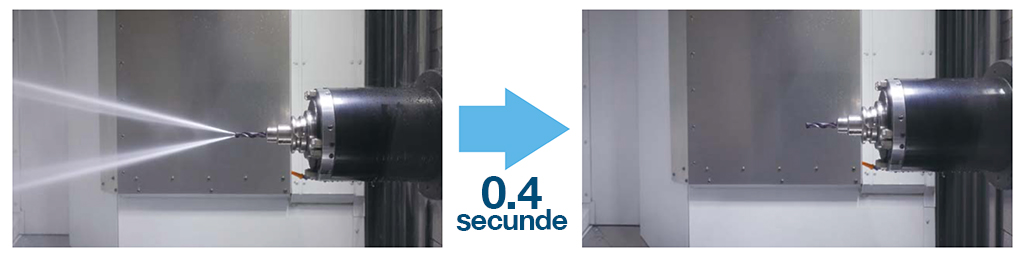
Timp de aspirare a lichidului de răcire: 0,4 secunde*1 *1. Timpul de aspirare a lichidului de răcire variază în funcție de sculă.
Timpi mai scurti de indexare a mesei de lucru
Timpul de indexare a tabelului este scurtat de funcția SERVONAVI Rotary Axis Inertia Auto Setting.
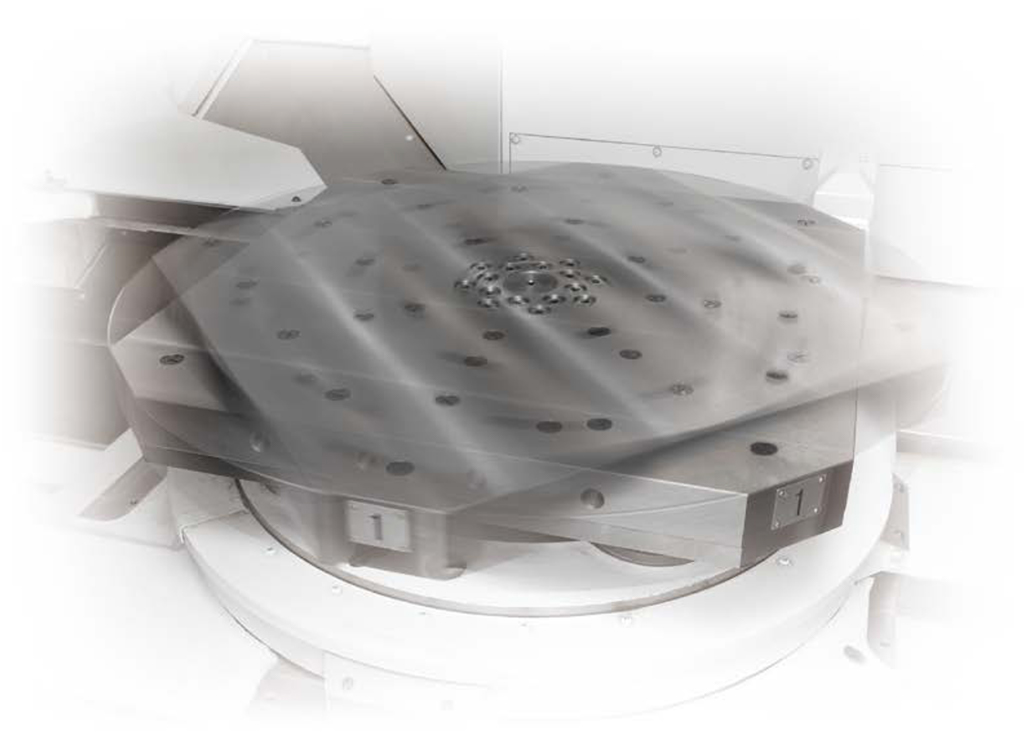
Timp de indexare [indexare de 1 grad]
1,6 sec/90°2 20% reducere (comparativ cu modelul anterior)
Timp de indexare [indexare de 0,001 grade] 1,4 sec/90°2 44% reducere (comparativ cu modelul anterior)
Operații cu viteză mare
Curse rapide | 60 m/min (X-, Y-, Z-axis) |
Accelerații | 0.7 G (max) |
Schimbare Scule | 2.0 sec (T-T) / 3.7 sec (C-C) / 3.7 sec (CTC min) |
Schimbare Palet | 12 sec / 13 sec |
Centru Orizontal prelucrare MA-600HIII cu evacuare de șpan care mărește timpul de funcționare productiv
Cu acoperire simplă a spațiului de lucru și aplicații ranforsate cu lichid de răcire, evacuare eficientă a așchiilor și posibile aplicații pe termen lung
Doar capacul unic de călătorie pe axa Z și capacele telescopice netede pe axa X,Y suprimă acumularea de așchii. Mai mult, la prelucrarea uscată fără lichid de răcire, este posibilă spălarea doar a zonei inferioare a spațiului de lucru cu lichid de răcire. Spălarea în mașină previne zonele probabile de acumulare de așchii, prin curățarea așchiilor pentru a menține ciclurile de producție pe termen lung.
Descărcarea așchiilor și spațiul de lucru conceput pentru a preveni acumularea de așchii
Lichid de răcire pentru spălarea în mașină: 450 L/min (îmbunătățire cu 18% față de mașina anterioară).
Spațiul de lucru mai puternic pentru spălarea zonei inferioare și transportorul cu balamale îndepărtează fără probleme lichidul de răcire mare și așchiile acumulate din mașină.
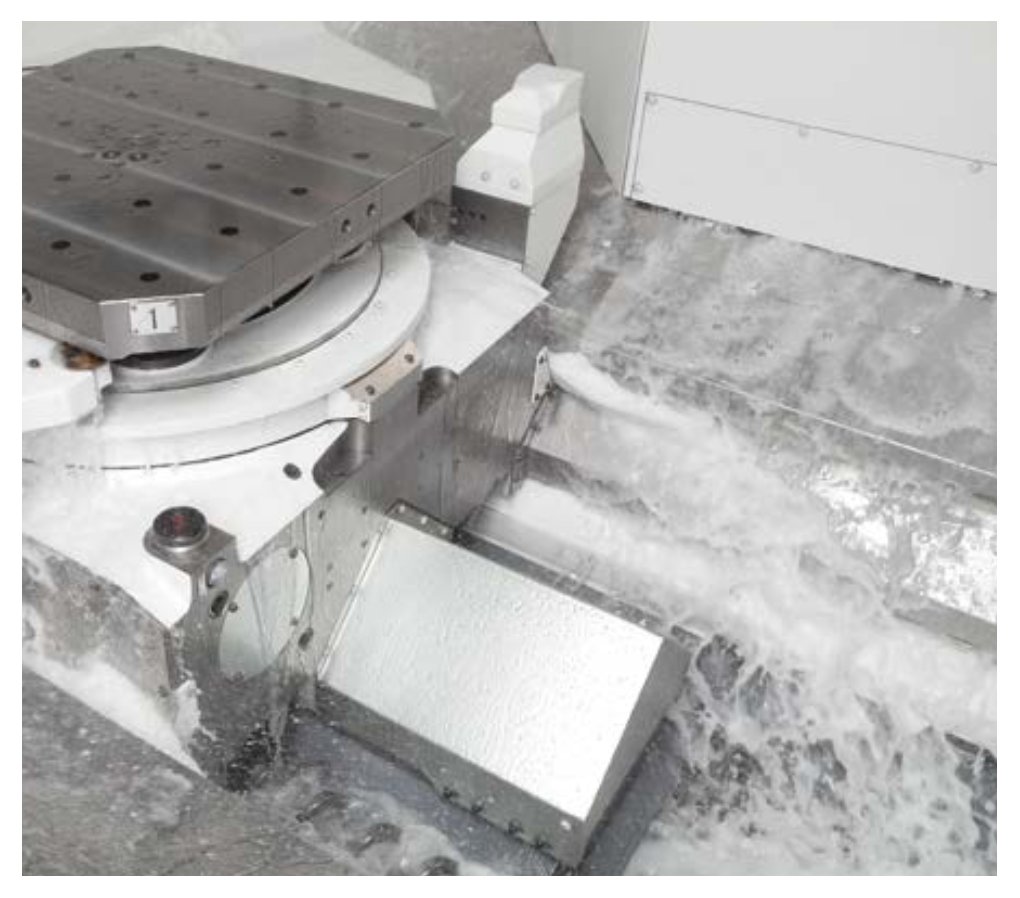
Din zona superioară a spațiului de lucru, un sistem de răcire pentru duș (opțional) și lichidul de răcire de la capacele telescopice pe axa X,Y elimină acumularea de așchii.
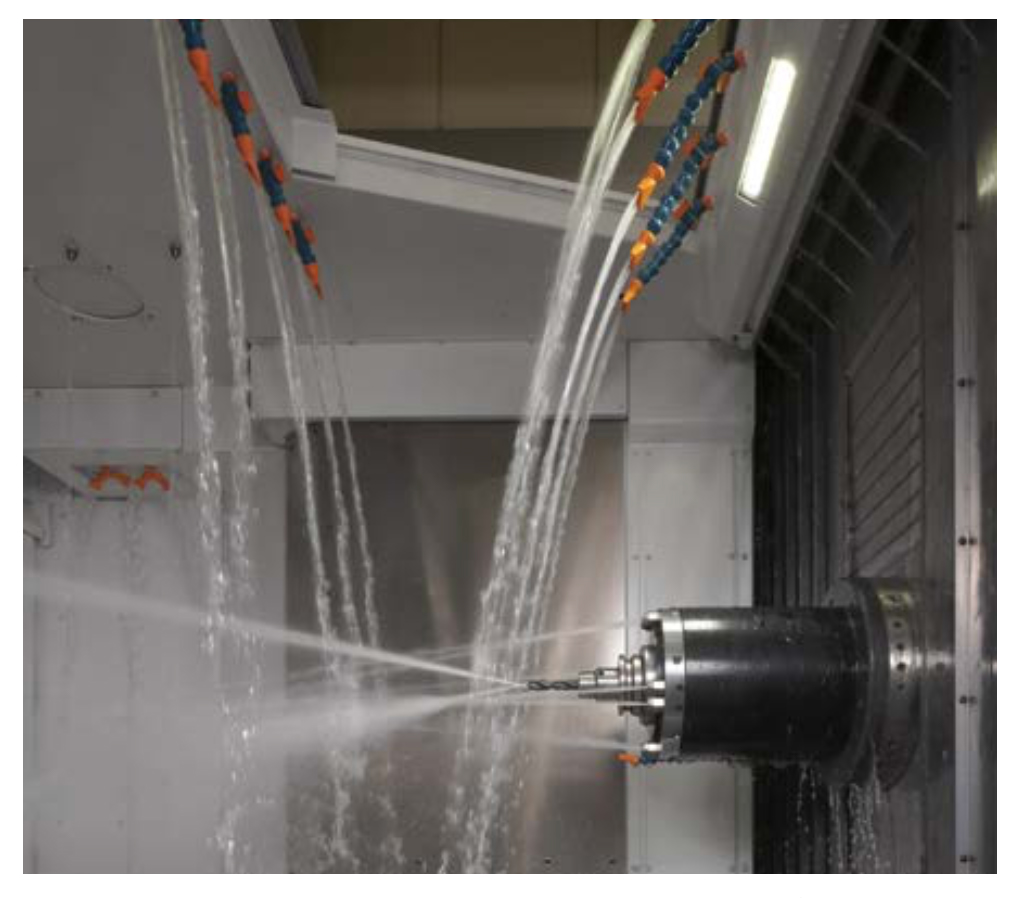
Prevenirea acumulării de așchii cu capace telescopice netede pe axa X, Y și capac unic din oțel inoxidabil pe axa Z
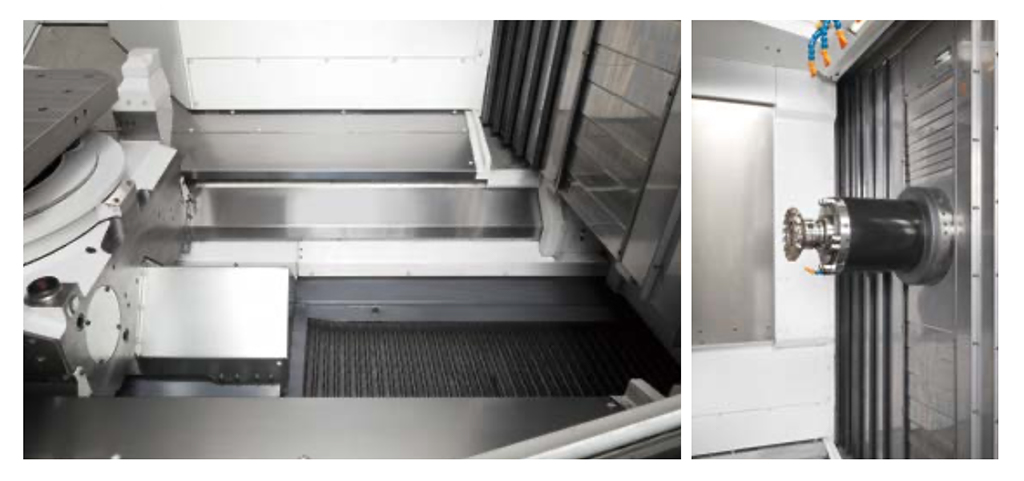
Capacele plate din spațiul de lucru previn acumularea așchiilor
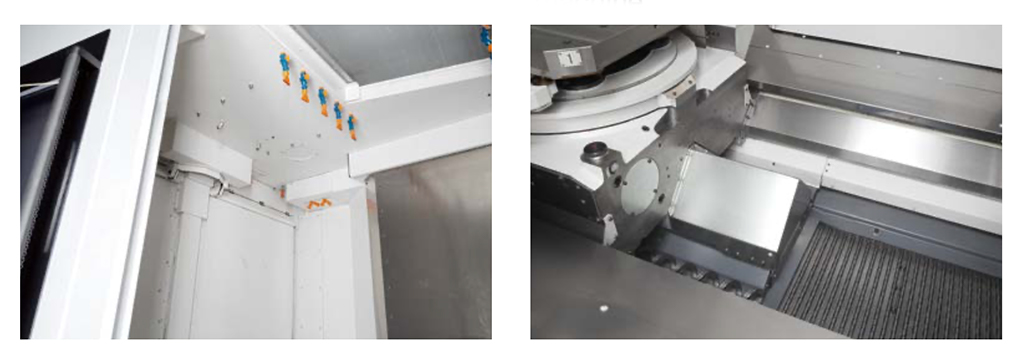
Designul jgheabului central îmbunătățește cantitatea mare de așchii din mașină
Descărcarea așchiilor în afara mașinii
Opțional, sunt disponibile un transportor de așchii care evacuează așchii în exteriorul mașinii și un rezervor fără reziduri (opțiune recomandată) care colectează eficient rezidurile din prelucrare.
Centru Orizontal prelucrare MA-600HIII cu rezervorul „Sludgeless Tank” asigură prelucrări precise pe toată durata de producție
Reduce cumularea de reziduri în rezervorul cu lichid de răcire. Reducerea dramatic frecvența lucrărilor de curățire a rezervorului.
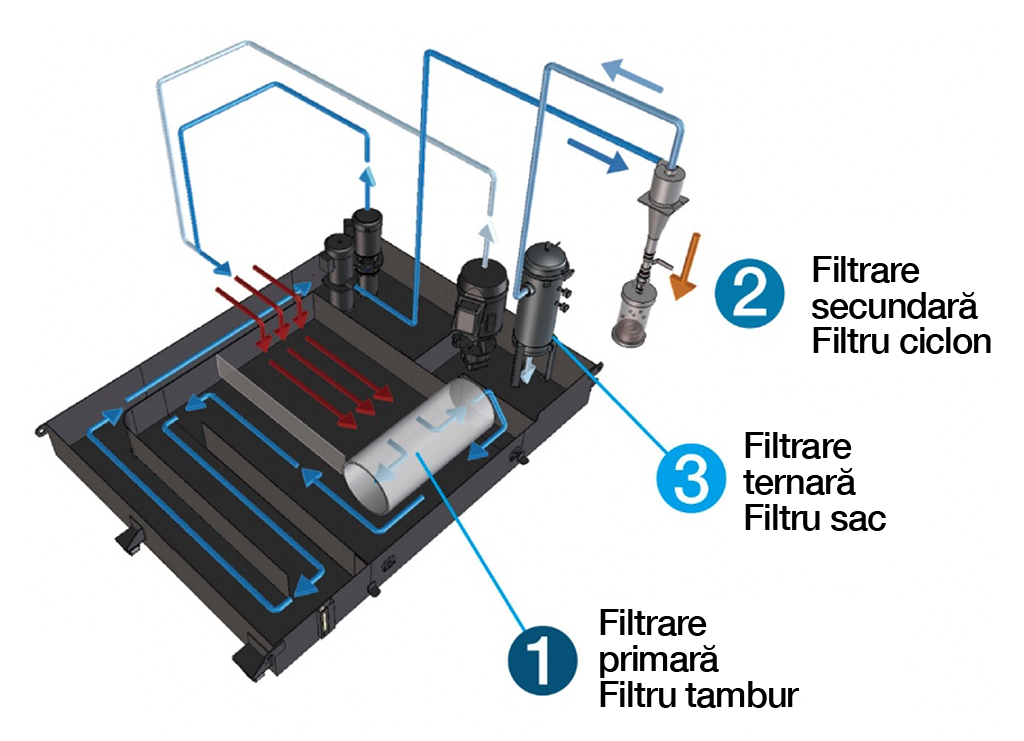
Îndepărtarea rezidurilor din lichidul de răcire, impact mai mic asupra mediului la evacuarea lichidului de răcire
Eliminare reziduri 99% (aliaje) 97% (aluminum)
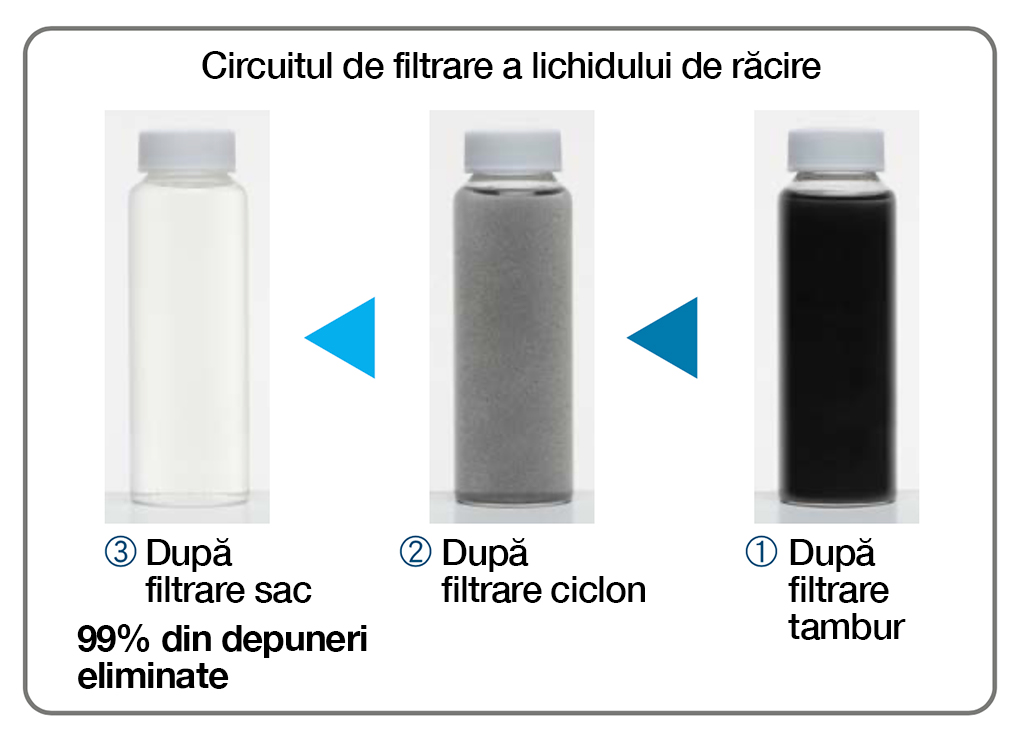
Nu este necesară curățarea rezervorului timp de doi ani (date reale de pe mașini Okuma)
Fluxul unidirecțional al lichid-ului de răcire în rezervorul elimină depunerile, de asemenea, deteriorarea lichidului de răcire din cauza stagnării. Frecvența de înlocuire a lichidului de răcire este mult redusă, iar impactul asupra mediului este mai mic atunci când cantitățile de lichid de răcire sunt reduse.
Menținerea arborelui principal curată
Cele trei nivele de filtrare din rezervorul fără depuneri și aspirația lichidului de răcire din interiorul arborelui reduc rezidurile de pe conicitatea axului și astfel prelucrarea defectuoasă.

Compact—integrat cu rezervorul lichididului de răcire prin arborele principal
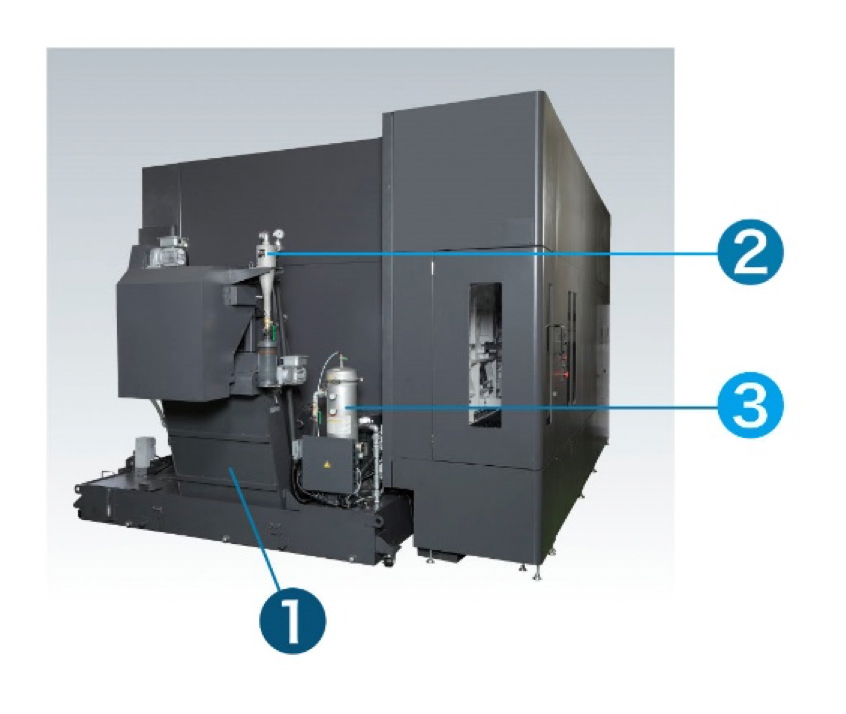
Rezervorul lichiduli de răcire prin arbore este integrat, iar încălzitorul / răcitorul de lichid de răcire (opțional) poate fi montat pe rezervor, economisind spațiu.
Suport de automatizare pentru a îmbunătăți în continuare productivitatea
Suport flexibil de automatizare
Echipat cu un număr mare de porturi de fixare prin paleți (opțional)
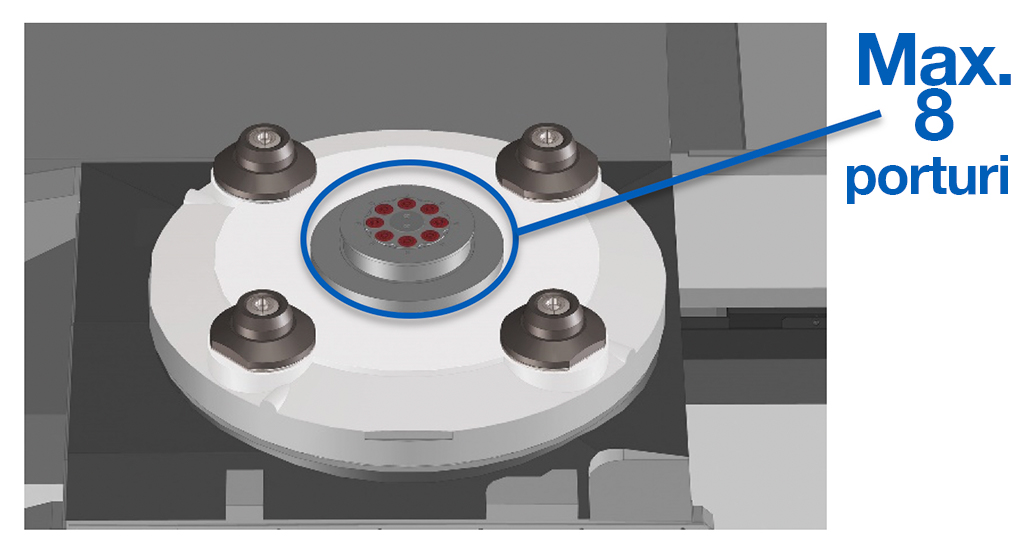
Baza de paleți a stației de configurare poate fi echipată cu până la 16 porturi de fixare pentru presiune hidraulică și pneumatică, iar baza de masă pentru spațiul de lucru poate avea până la 8 porturi pentru aplicații flexibile de automatizare.
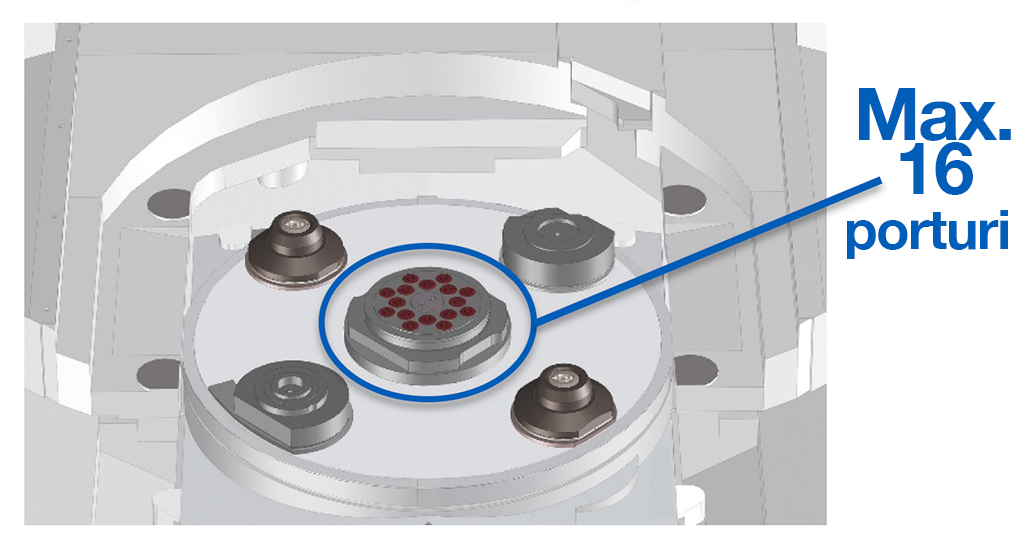
Circuitele hidraulice care tind să fie complicate pot fi simplificate, iar proiectarea dispozitivelor de prindere automată devine ușoară. Clienții beneficiază de mai multă libertate în sistematizare și în satisfacerea nevoilor mai diverse de automatizare.
Configurare automată Rotire palet stație (opțiune)
Această caracteristică rotește automat paletul stației de configurare în trepte de 90° prin apăsarea comutatorului cu picior. Eficiența operatorului a fost îmbunătățită, iar încărcarea/descărcarea parțială robotizată se poate face din mai multe dispozitive de fixare.
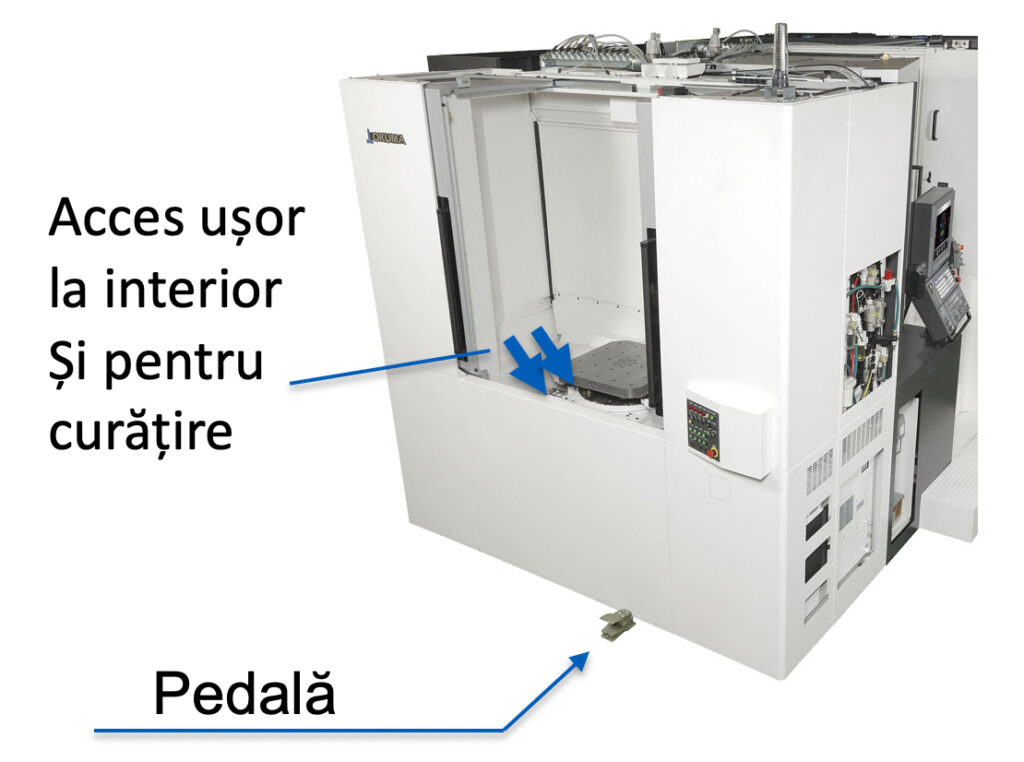
Producție flexibilă de aplicații mari pentru piese de prelucrat
O gamă impresionantă de sisteme de automatizare
Sisteme flexibile APC
APC-urile multipaleți permit operatorului să configureze un număr mare de piese de prelucrat și să folosească timpul suplimentar disponibil pentru alte lucrări. Configurațiile la sfârșitul zilei pentru operațiuni nesupravegheate sunt, de asemenea, un avantaj.
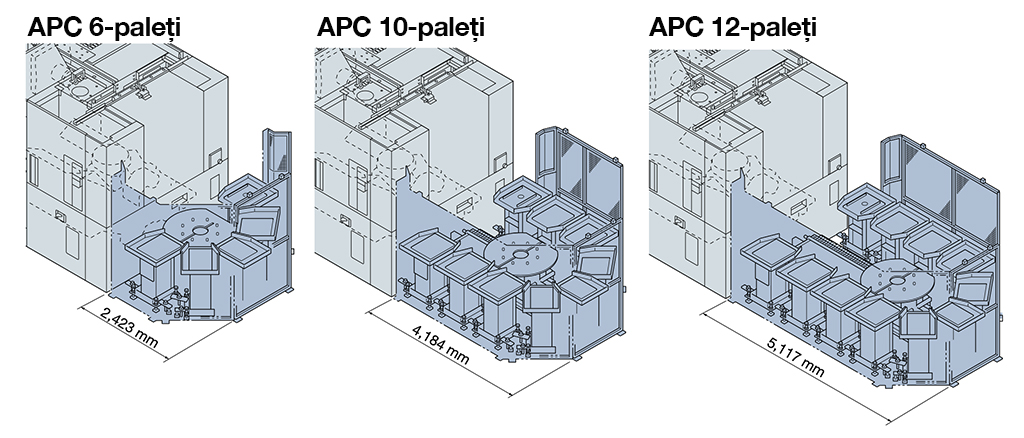
- APC multipaleți se conectează la APC standard cu navetă rotativă cu 2 paleți
- Timpul de schimbare a paleților este același ca în APC standard
- Poate fi adaptat pentru a se potrivi cu tipul echipamentelor și tipul de producție
Multi-Pallet Tower APC*
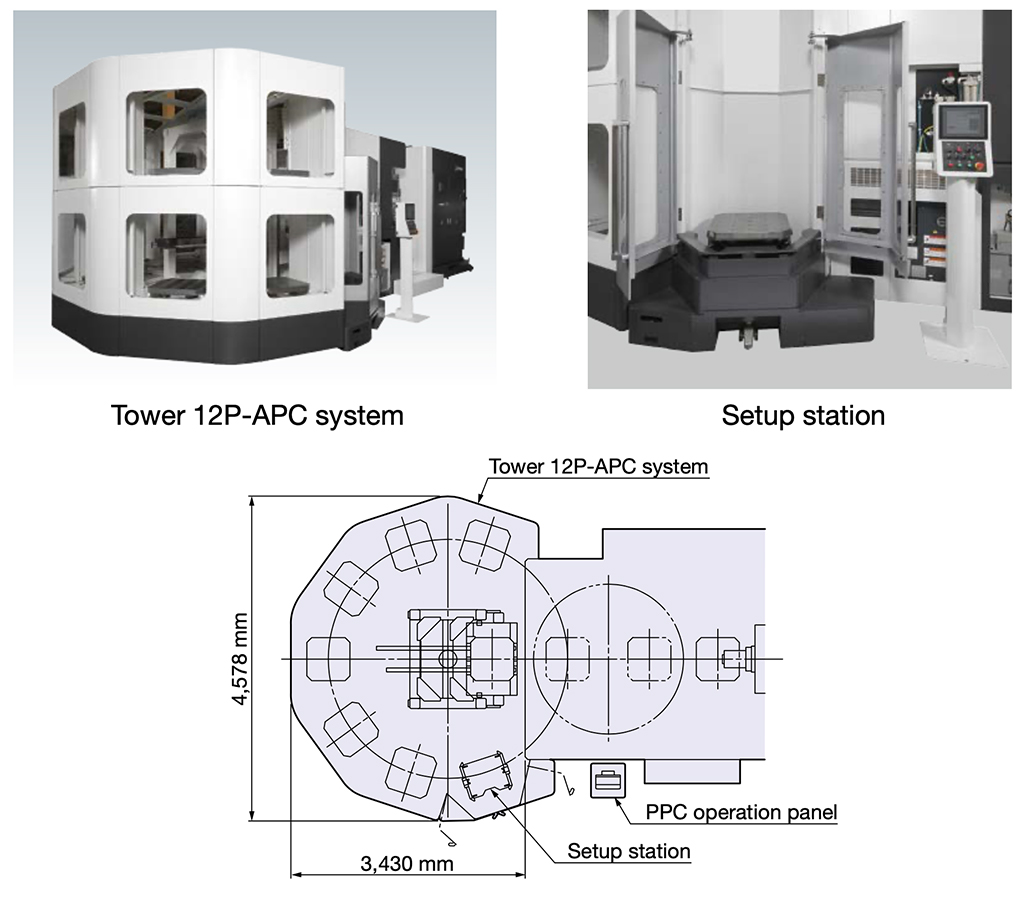
Schimbare automată de scule – ATC
Numărul standard de scule care pot fi depozitate este de 60. Sisteme flexibile de depozitare a sculelor de mare volum disponibile pentru adăugarea mai multor tipuri de piese de prelucrat. Magazinele Matrix stochează un număr mai mare în aranjamente compacte și rapide de schimbare a sculelor.
● Magazie Matriceală: Timp de pregătire a sculei
Minim: 12 secunde (mai multe module: 19 secunde)
Capacitate scule | Tip magazie |
40 tools, 60 tools (standard) | Magazie cu lanț |
81 tools, 111 tools, 141 tools, 171 tools | Magazie matriceală (171 scule) |
195 tools, 225 tools, 255 tools, 285 tools | Magazie matriceală (285 scule) |
320 tools, 400 tools | Magazii multiple |
Tehnologie avansată — eficientă pentru atelierele de prelucrare
Servocontrol optimizat SERVONAVI
SERVONAVI AI (Identificare automată)
● Setare automată a greutății de lucru
Timpul ciclului scurtat cu o accelerare mai rapidă
● Setarea automată a inerției axei rotative Menține precizia ridicată și mișcările stabile
SERVONAVI SF (Reglare fină a suprafeței)
● Reglare automată a vârfului inversării
Mentine precizia prelucrarii si calitatea suprafeței
● Ajustarea automată a vibrațiilor contribuie la o durată de viață mai lungă a mașinii CNC
Sistem de prevenire a coliziunilor (opțional) Prevenirea coliziunilor
Prelucrare Navi M-i, M-gII+ (opțional) Căutare condiții optime de așchiere frezare
Hyper-Surface (opțiune) Compensare automată a datelor de prelucrare
Îmbunătățirea suplimentară a calității suprafeței prelucrate prin noua compensare a datelor de prelucrare.
Prin suprimarea dungilor și a neregulilor de margine cauzate de datele de prelucrare CAM, timpul de lustruire manuală poate fi, de asemenea, redus. În plus față de Controlul adaptiv al accelerației pentru suprafața sculptată cu Super-NURBS anterioară, noua funcție Hyper-Surface compensează automat erorile de poziționare a muchiilor ale datelor de prelucrare ieșite din CAM sau traseul de tăiere adiacent, menținând în același timp precizia formei.
Așchiere-strunjire (opțiune)
Timp de livrare mai scurt cu prelucrarea intensivă a procesului
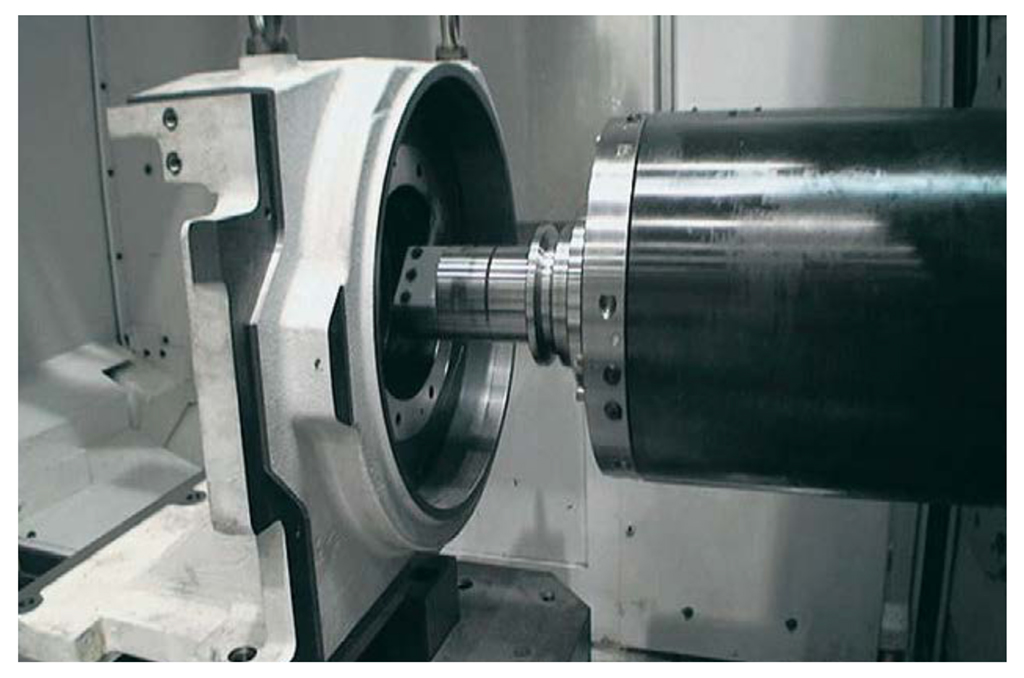
Rotirea arborelui și sculei permite așchierea ca un strung.
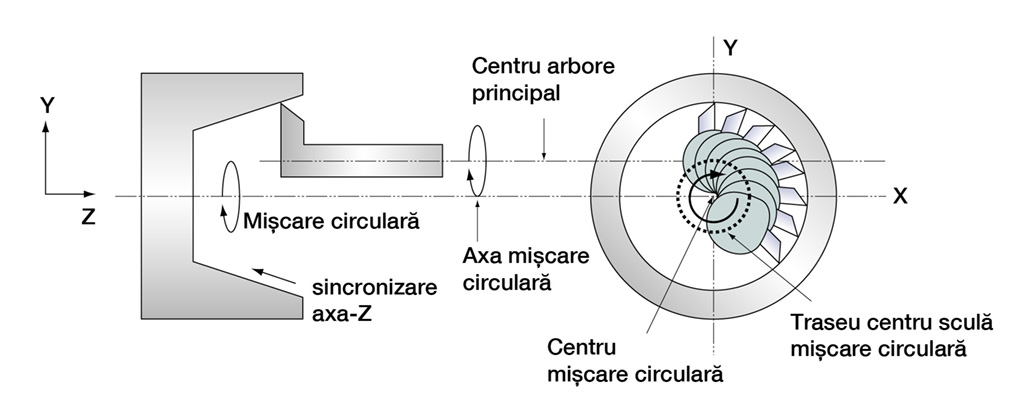
● Posibile, de asemenea, filetarea
● Realizarea alezajelor cu diferite diametre — cu o singură unealtă
● Așhiere internă / externă cu diametre mari de scule supradimensionate ATC
Diagnosticare mașină AI (opțiune)
Tehnologie de diagnosticare a mașinilor-unelte cu inteligență artificială (AI)
Cu întreținerea predictivă, preveniți oprirea mașinii la timp
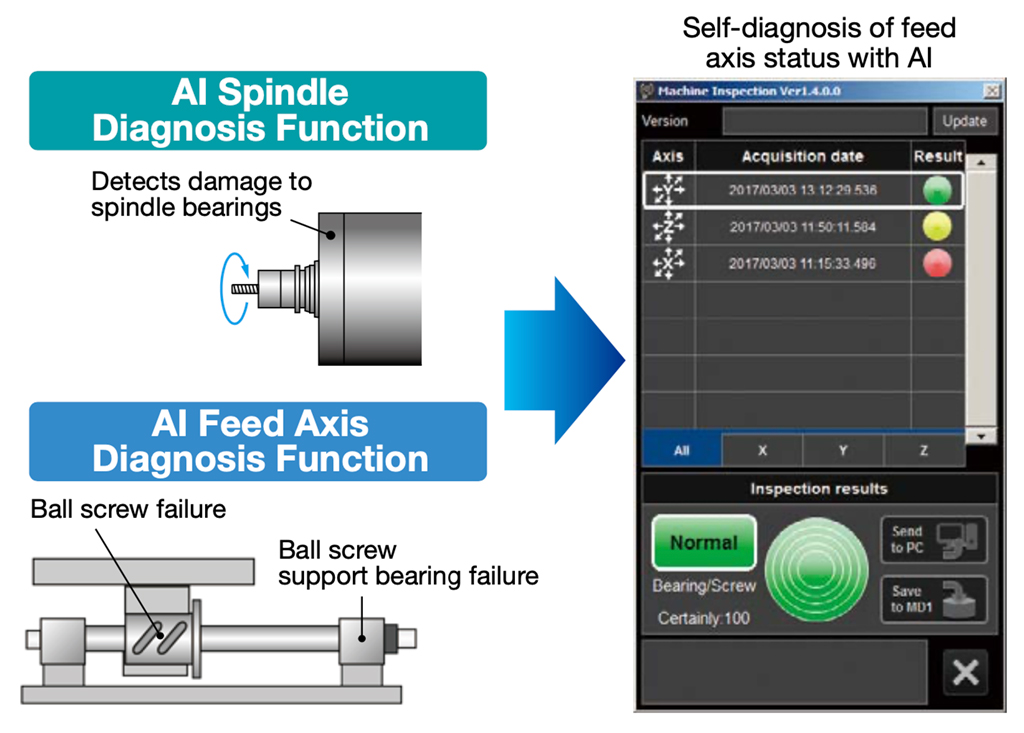
Controlul echipat cu inteligență artificială de la Okuma diagnostichează prezența sau absența anomaliilor în axul mașinii și axele de avans și identifică orice nereguli găsite.
Timpul de nefuncționare de la oprirea mașinii este minimizat, astfel încât beneficiile sunt operațiuni extrem de precise, productive și stabile pe termen lung. Operatorii înșiși pot diagnostica cu ușurință mașina urmând instrucțiunile simple ale ecranului de pe controlul Okuma.
Design Inteligent
Acest centru de prelucrare orizontal de ultimă generație cântărește 25.000 kg, asigurând stabilitate structurală și operațiuni de prelucrare cu precizie consistente pe termen lung. Această mașină are un spațiu de lucru mai mare decât predecesorul său, cu capacități suplimentare de deplasare pe axe extinse cu 100mm. În plus, MA-600HIII poate efectua operațiuni automate de schimbare a sculei în mai puțin de patru secunde!
Au fost aduse, de asemenea, îmbunătățiri suplimentare tehnologiei Okuma de management termic, lider pe piață, inclusiv reducerea deformărilor termice a mașinii la o schimbare dimensională îmbunătățită de 7μ (șapte microni) pe o perioadă de 24 de ore. Acest lucru este deosebit de eficient atunci când se confruntă cu variații severe ale temperaturii ambientale din fabrică.
Sisteme nou de gestionare a șpanului și a lichidului de răcire
Okuma MA-600HIII are un sistem îmbunătățit de gestionare a lichidului de răcire, răcire pentru șurubul cu bile pentru axele X, Y și Z, un design îmbunătățit al spațiului de lucru pentru a preveni acumularea de așchii și o funcționalitate îmbunătățită de evacuare a șpanului. Acest nivel de inovație crește timpul de funcționare și permite perioade lungi de funcționare neîntreruptă a mașinii.
Tehnologia cu totul nouă a rezervorului fără reziduri este posibilă cu modelele noi sofisticate de filtrare și de scurgere a lichidului de răcire pentru a reduce depunerea amestecului în fundul rezervorului de primire. Această nouă tehnologie reduce nevoia de curățare îndelungată a rezervorului și oferă un timp de funcționare crescut al mașinii.
Prietenos cu automatizările
Designul flexibil al MA-600HIII permite o varietate de aplicații de automatizare. Zona spațiului de lucru poate echipa până la șapte porturi de încărcare/descărcare parțială sau până la opt porturi de clemă de susținere a lucrării, ceea ce poate ajuta la eliminarea necesității unor aranjamente complicate de circuite pentru aplicațiile hidraulice. Până la 16 porturi sunt disponibile în stația de configurare a mașinii, extinzând capacitatea pieselor și posibilitățile pentru aplicații robotizate.
Echipat cu o listă impresionantă de caracteristici standard, Okuma MA-600HIII este un plus de încredere și profitabil pentru orice atelier. Contactați-ne pentru mai multe detalii și pentru a solicita o ofertă.
Video Prezentare // EMO 2021
Specificații Tehnice
Dimensiuni Masă [mm] | 630 x 630 |
Greutate [kg] | 25,000 (55,000) |
Viteze Arbore Principal [rot/min] | 6,000 [10,000, 12,000, 15,000, 20,000] |
Nr. de Scule | 60 [81, 111, 141, 171, 195, 225, 255, 285, 320, 400] |
Putere Motor [kW] | 30/22 [45/37], [37/26], [26/18.5] |
Curse Axe [mm] | X: 1,050 / Y: 900 / Z: 1,000 |
Opțiuni / Automatizări | Automatizare Tower APC |